In this issue, we focused on the sources of faults that arise during the assembly and disassembly of pumps. Failure to pay attention may result in damage to the gasket, body and connections (electrical, fuel).
Assembly errors
Tightening Without Holding
When tightening the fuel connection line on gear ring pumps, it is quite common for the nipple connected to the pump body to not lock. Failure to hold the coupling causes the entire pump cover to rotate along with the connections in the body. Rotation of the lid often causes the sealing ring to shift or be damaged and leaks to occur.
There are markings on the E2T and E3T fuel pumps. They must be opposite each other. Inconsistency in the location of the features indicates improper assembly of the pump and its damage.
CAUTION. When tightening the connecting cable, the lower hexagon of the fuel pump must be locked. Otherwise, leaks may occur. A leaking pump is a fire hazard.
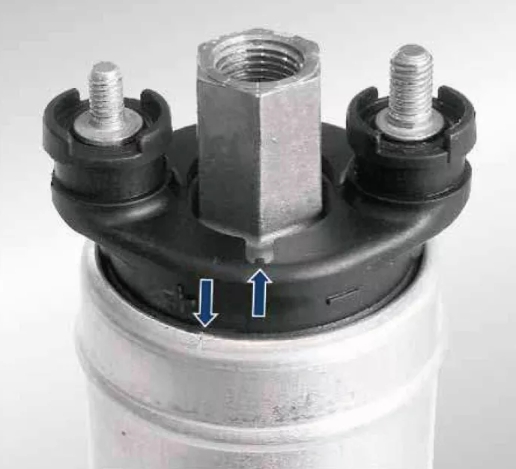
Contact Corrosion
Improper assembly or faulty repairs to the pump can cause pitting corrosion. It is not recommended to install galvanized steel clamps without insulation on the aluminum pump body. The appearance of electrolyte where the body contacts the uninsulated clamp will cause corrosion.
CAUTION. The aluminum pump body must not come into direct contact with the galvanized surface. This may result in pitting corrosion and, consequently, leakage of the housing. A leaking pump is a fire hazard.
Force damage
Casing Damage
Cracks and leaks may occur in the pump casing if the pump is dropped or if care is not taken when repairing the fuel system.
Damage to connections
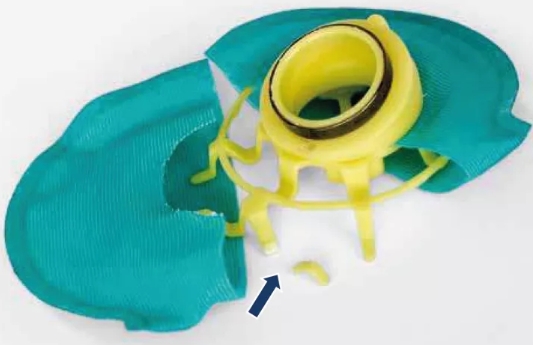
Incorrect assembly/disassembly can damage electrical connections and fuel connections. Do not use force when connecting the power lines and fuel line.
Damaged filters
In-tank pumps have a mesh filter on the suction side and some filters also have stiffening ribs. Incorrect installation can damage the filter and fins, and the resulting debris or debris can clog the fuel pump.
Fill level sensor broken off
In some fuel delivery modules, the mechanical system of the fill level sensor has a damping device. Never move the sensor by hand as it may break off.
Fill level sensor is bent
The arm of the fill level sensor can be bent if installed incorrectly. Bending may cause incorrect fuel quantity indications.
